Achieving Tooling Success Through Finite Element Analysis
The engineers at Hi-Tech Plastics and Molds use creative genius and scientific molding to execute your design successfully, from art to production part. Utilizing methods like Finite Element Analysis helps our engineers achieve 1st Generation tooling success for intricate designs.
A manufacturing client conceptualized a plastic molded part for bindings while skiing at California’s Mammoth Mountain Ski Area during their Christmas holiday break in 2010. They knew the disc needed to be durable and made to precise tolerances, and from materials exhibiting the right properties for strength and cold weather resistance.
The Challenge: Mold Design for Ski Binding Parts
After creating a preliminary drawing, the client tried creating a mold thick enough for their part but was unsuccessful. They contacted Hi-Tech for assistance and submitted their 3D drawing to us for review.
The Solution: Scientific Molding & Engineering
The engineering team at Hi-Tech takes all the necessary steps to get the right outcome on 1st generation tooling. This product’s scientific molding process involved multiple rounds of finite element analysis and 3D simulation before cutting the steel into molds.
- Step 1: We applied Finite Element Analysis “FEA” to 3 iterations of design. This process helped us determine which result would be the optimum 1st generation design theoretically.
- Step 2: Another round of Finite Element Analysis helped find stresses in the design, confirm optimum part geometry, and determine material selection before designing the mold.
- Step 3: Our Design for Manufacturability phase included 3D modeling and complete Mold Optimization simulation studies using Autodesk Moldflow Insight. The objective was to evaluate the filling pattern and optimize the cooling layout to provide uniform temperature and minimize warpage.
- Step 4: The engineering team used scientific molding studies to validate the theoretical design. Through this process, we optimized processing parameters and narrow the numerous options. Scientific molding helps us achieve a best-case outcome with 1st generation tooling before mold production begins.
Finite Element Analysis of Part Stress After Molding with Specific Gate Location
Phantom lines on the drawing provide additional clarity in the location of the highly stressed areas. The dark blue regions of the part are a good indication of where material may be removed by coring if a weight reduction is desired in the part under these conditions.
Complete Mold Optimization Study Using Autodesk Moldflow Insight
This plot shows how shrinkage differences in the part affect the warpage. Based on the scale, the analysis shows the shrinkage differences from the perimeter of the part to the center have an impact on the part warpage.
This plot shows how shrinkage differences in the part affect the warpage. Based on the scale, the analysis shows the shrinkage differences from the perimeter of the part to the center have an impact on the part warpage.
The Results: Prototype Testing & Product Launch
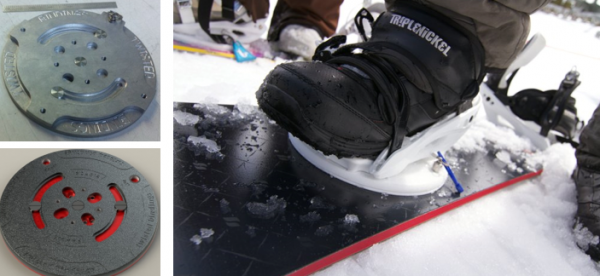
After narrowing down all options, we developed three prototypes for the injection molded ski binding part. Prototype testing occurred at Mammoth Mountain Ski Resort and Mt. Hood, Oregon.
Prototype Testing Timeline
- March 4-6, 2011: Testing for Prototype I, made from aluminum.
- March 31-April 5, 2011: Testing for Prototype II, machined from GF Nylon sheet, was tested at Mammoth Mountain Ski Area.
- May 20-22, 2011: Testing for Prototype III, made using Selective Laser Sintering with epoxy inserts.
Ultimately, the solution for molding the binding component was utilizing selective laser sintering with epoxy inserts. The final design was ordered on June 21, 2011 with a production-ready product target of August 2011.
The final prototype was tested at Mt. Hood, Oregon and considered a great success. The client’s final product launched on August 27, 2011, which was within their targeted deadline.
Your Trusted Partners in Injection Molding Design for Manufacturability
Our engineering team consists of in-house designers and molders, along with a nationwide network of thermoplastic injection molding experts. Using our collective scientific molding expertise and high quality standards, we help clients achieve success in their part design. Visit our work gallery to see more examples of competed projects or contact us to discuss your design concept